Essay/Term paper: Tqm
Essay, term paper, research paper: Management
Free essays available online are good but they will not follow the guidelines of your particular writing assignment. If you need a custom term paper on Management: TQM, you can hire a professional writer here to write you a high quality authentic essay. While free essays can be traced by Turnitin (plagiarism detection program), our custom written essays will pass any plagiarism test. Our writing service will save you time and grade.
Introduction
The purpose of this report is to critically analyse, evaluate and discuss related management issues conducive to the development of a total quality management environment within an organisation. This shall be done by critically analysing the case study of Agrotran Ltd. This report will discuss the role and application of quality management systems in organisations, debate and recommend a suitable way forward for Agrotran Ltd.
The issues concerning Agrotran Ltd
Agrotran is a small engineering company specialising in the manufacture of farming equipment. The four owners have recently sold out to the Nat-truk Group a manufacturer of specialist trucks and transport"s. The original owners set up Agrotran when they were made redundant from a large engineering company. They have a good working relationship, working well as a team and intimate knowledge of their business. They also have a laid back style of management.
There are a number of issues that have arisen since the take-over.
Nat-truk are seeking to be included on the Ministry of Defences approved supplier list. This means that they and Agrotran need to achieve ISO 9000 certification although this was argued against by one of the former owners during the take-over negotiations. This has been seen as an imposition of extra cost and bureaucracy on Agrotran by Nat-truk.
Nat-truk has also introduced its own employees to Agrotran. This has resulted in fights breaking out between Agrotran and Nat-truk workers. The bases of these arguments are over communication problems involving processes, standards and specifications. This has resulted in some of Agrotran"s best customers complaining about quality. One of the original owners Tom Smith has laid the blame on the extra procedures and paperwork choking up the system causing delays and loss of control.
The role and purpose of quality management systems
The role and purpose of quality management systems is to reduce the dependence on 3rd party audits and to provide a documented management system, which will provide clearer working procedures, improve quality control and efficiency. The Key features of a quality management system are the documented policy manuals and procedures on which the company could be audited. These policies and procedures should allow flexibility and adapt to change but always regain control. The objective of the quality management system ISO9000 "is to give purchasers an assurance that the quality of the products and/or services provided by a supplier meets their requirements" (Dale 1999). With this the company would seek to widen its customer base, as the customer is given an assurance of quality and the need for them to carry out their own audit is not required unless their own standards are higher than the requirements of ISO9000. "A number of major purchasers use this registration as the "first-pass" over a supplier"s quality system" (Dale 1999). ISO9000 can also be used as the foundation for the introduction of TQM.
The application of quality management systems
The application of the ISO9000 series of standards can be used in three ways (Dale 1999).
1. To provide guidance to organisations, to assist them in developing their quality systems
2. As a purchasing standard (when specified in contracts)
3. As an assessment standard to be used by both second party and third party organisations.
The ISO9000 series consists of ISO9000, ISO9001, ISO9002, ISO9003, and ISO9004
ISO9000 – Guidelines for Selection and Use and ISO9004 Guidelines for Specific Applications are only used as guidelines and to explain the application of ISO9001, ISO9002 and ISO9003.
ISO9001 Model for Quality Assurance in Design, Development, Production, Installation and Servicing
Covers 20 principal clauses which are of a management or operational nature
Management/macro requirements Operational requirements
1. Management responsibility
2. Quality system
3. Contract review
5. Document and data control
17. Internal quality audits
18. Training
4. Design control
6. Purchasing
7. Control of customer-supplied product
8. Product identification and traceability
9. Process control
10. Inspection and testing
11. Control of inspection, measuring and test equipment
12. Inspection and test status
13. Control of non-conforming product
14. Corrective and preventive action
15. Handling, storage, packaging, preservation and delivery
16. Control of quality records
19. Servicing
20. Statistical techniques
The Institute of Management
ISO9002 includes all of ISO9001 except design control
ISO9003 includes all of ISO9001 except design control, purchasing, process control and servicing
Development of a Total Quality Management within an organisation
If an organisation is to develop Total Quality Management then it must first understand what it is and how it has been developed. Which is easier said than done, as there are many different definitions of quality and how to achieve it. The main approaches in quality originate from Crosby, Deming, Feigenbaum, and Juran.
Crosby
Crosby (1979) defines quality as "conformance to requirements", and his approach consists of :
 Quality means conformance, not elegance.
 It is always cheaper to do the job right the first time.
 The only performance indicator is the cost of quality
 The only performance standard is zero defects
 No such thing as a quality problem
This achieved through Crosby"s 14-step quality improvement programme.
Responsibility is allocated as follows
 The Quality professional – a moderate amount
 The hourly workforce – a limited role, reporting problems to management
 Top management – an important role
Deming
Deming defines quality in terms of quality of design, quality of conformance, and quality of the sales and service function.
Deming"s approach is base on PDCA (Plan, Do, Check, Action) and his philosophy for improving quality is summarised in his 14 points for management. He also points out the seven "deadly diseases" of western management and organisational practice.
Deming (Dale 1999) states that "quality and improvement is the responsibility of all the firm"s employees: top management must adopt the "new religion" of quality, lead the drive for improvement and be involved in all stages of the process".
Feigenbaum
Feigenbaum was the first to use the term "total quality control". Feigenbaum (1991) has defined it thus "Total Quality Control is an effective system for integrating the quality-development, quality maintenance, and quality-improvement efforts of the various groups in an organisation so as to enable marketing, engineering, production, and service at the most economical levels which allow for full customer satisfaction".
Feigenbaum"s approach is to help companies design their own system more than creating managerial awareness of quality. His contribution to the subject of the cost of quality is that "quality costs must be categorised if they are to be managed." The three major categories being, appraisal costs, prevention costs, and failure costs which make up the Total Quality Costs.
Feigenbaum rests most responsibility with management saying that management must commit themselves:
 To strengthen the quality improvement process itself
 To making sure that quality improvement becomes a habit
 To managing and cost as complementary objectives
Instead of providing a step by step plan Feigenbaum provides ten benchmarks for total quality success.
Juran
Juran (1988) defines quality as "fitness for use", which he breaks into quality of design, quality of conformance, availability, and field service. Juran"s approach is to improve quality by increased conformance and decreased costs of quality by the setting of yearly goals. Juran has also developed a quality trilogy (quality planning, quality control and quality improvement) and a ten-point plan to summarise his approach.
Juran gives the main responsibility to the quality professionals
There are many others, who have added to the development of TQM such as Ishikawa,
Taguchi, Shingo, Peters, Dale, and Oakland etc.
Defining TQM
Total Quality Management is defined in the American Society for Quality Control"s Bibliography as "TQM is a Management approach to long-term success through customer satisfaction…based on the participation of all members of an organisation in improving processes, products, services and the culture they work in" (Bemowski 1992 Cited by Hiam 1994)
"Actions taken throughout the organisation to increase the effectiveness and efficiency of activities and processes in order to provide added benefits to both the organisation and it"s customers" (ISO8402)
TQM is a style of managing which gives everyone in the organisation responsibility for delivering quality to the final customer, quality being described as "fitness for purpose" or delighting the customer". TQM views each task in the organisation as fundamentally a process which is in a customer supplier relationship with the next process. The aim at each stage is to define and meet the customer"s requirements in order to maximise the satisfaction of the final consumer at the lowest possible cost. (The Institute of Management)
Juran, in an interview (Gordon 1994), claims that TQM involves the use of any means to achieve World-Class Quality, and acknowledges that there is no clear definition of TQM.
These are just a few definitions of TQM. Each guru, each consultant has their own depending on their particular bias. A company undertaking TQM will probably arrive at its own version, which is fine as not all the tools, techniques and philosophy will be relevant to them and they will have their own bias, but any outsider should recognise it as TQM.
TQM adoption and development
Although there are many differences in the philosophies of the experts there are basic key elements common to each that a company must address when embarking on the adoption of TQM
Planning and Organisation
 Development of a long term strategy
 Development of polices
 Building product and service quality into designs and processes
 Development of procedures
Using tools and Techniques
The correct selection of tools and techniques to enable the process of continuous improvement. The company needs to identify the priority of each tool it is to introduce, explain why they are required. The use of these tools will not be successful until they are part of the every day behaviour of the company. Therefore an appropriate time should be given between introductions or people will be trying to learn a new tool before they have got to grips with the last one.
Education and Training
This has to be company wide with each person receiving a level of training and education that will enable them to carry out and understand the quality tools, techniques and philosophy. This should be done through a training programme that best suit the needs of the company and employee.
Involvement
In this, employees are involved in the decision making that effect them and their function. The desired effect is to improve commitment, enrich their job, and benefit from their hands-on experience. This is normally done through Q.C."s. If employees are allowed to solve problems, they probably will, and engineers etc., can act more as consultants and spend less time fire fighting.
Teamwork
Teamwork requires effective communication and involvement. Teams can take many forms such as, Cross Functional Groups, Project Groups and Focus Groups. Roles, responsibilities and boundaries have to be clear with sufficient support from senior management.
Measurement and Feedback
Control Systems need to be set in place, to measure whatever you need to manage, whatever you need to improve. The control system must feed back the appropriate information to the relevant people in a timely fashion. The Measuring Systems need to be discussed with who is using them and who is being measured. If employees are taught SPC – and assess themselves, this should lead to greater commitment.
Ensuring the culture is conducive to continuous improvement activity
This is perhaps the most important element and needs to start at the top. If the senior management avoid getting involved and only pay lip service to TQM, or say one thing and act in a manner that is not conducive to TQM, then it is unlikely that the employees will commit themselves to TQM.
Another element common to TQM is the use of Self-Assessment Models and Quality Awards.
The most common used models are the Deming Application Prize, The European Business Excellence Model (Figure 1) and the Malcolm Baldrige National Quality Award. These are very useful tools in aiding TQM Development and Business Performance. The managers must have a firm grasp on what TQM is, as these models will not lead to it.
Figure 1 The EFQM model for business excellence, Kaye, Anderson (1998)
Once the company has an understanding of TQM. It should then carry out a health check to assess its situation. This review should be in the common understandable language of the participants, to avoid misunderstandings and so no one feels that they are being talked down, this should ensure greater participation. By asking questions such as:
 How far along the company is to TQM
 What does it still has to achieve
 What it will have to change with respect to the key elements of TQM
 What TQM evolutionary level best represents the company
 What level of TQM adoption the company is at
 What are the attitudes of the staff towards the company
The objectives of a health check should be to
 To give the company a starting point and subsequently measure change from that position.
 To identify issues
 To seek out hidden agendas and areas of resistance
 To establish priorities
Two guidelines that companies can use to assess their position in TQM terms are:
Dales (1999) "Four Levels in the Evolution of TQM" and Lascelles & Dales (1993) Levels of TQM Adoption (Figures 2 and 3). These models could also help in creating achievable targets e.g. Today where we are classed as uncommitted company and cover all the inspection requirements. In one years time we will be classed as a drifter and incorporate all of the Quality Control Criteria.
Figure 2 The four levels in the evolution of TQM (Dale 1999)
Figure 3 Levels of TQM adoption, Lascelles and Dale (1993)
Figure 4 The Quality Training Cycle
Once it has assessed its situation it can then plan out the appropriate steps and timescale it needs to achieve them. Each step should be taken as an identifiable project using the quality training cycle (figure 4)
The development of TQM in any company takes many years. It would be unwise for anyone to attempt the whole thing at once.
The Argument for TQM
There are many claims made for TQM by the myriad of consultants and gurus some of these claims can be quite wild, some consultants may try and sell TQM as a quick fix, this kind of claim does not help the serious teachers and users of TQM. The most recognisable advantages of TQM are:
 It helps provide the customer with a improved product or service
 The customer can be assured of a desirable quality standard
 It requires critical analysis of what you do and how you do it
 Standardises procedures that clarify employees tasks and roles
 Creates ownership and motivation in the work force thus improving effectiveness and efficiency
 Creates a corporate history that can be referred to through documents and records
 Cuts and improves training time through training records and reference manuals
 It requires improved standards, services and cost from suppliers
 Adoption of ISO9000, success in quality awards etc. improves the company profile and market potential
 Cuts the cost of wasted resources and materials
Criticisms of TQM
Those who argue against TQM such as Harari, Grossman, Grint from research carried out by Arthur D Little, Ernst & Young, Rath & Strong, McKinsey & Co & AT Kearney, point out that only 20-30% of TQM initiatives are successful. Therefore, it cannot justify itself as a success or worth the money.
The defenders of TQM explain this low success rate, as due to poor implementation, and that the critics and failures do not fully understand TQM, but a theory is no good unless it works in practice. Therefore, any company undertaking TQM could learn a lot from the critics, and possibly avoid the pit falls.
Harari (1992,1993) has pointed out his criticisms, which are common to most critics, in his "Ten Reasons TQM Doesn"t Work", and later adding an 11th:
1. TQM focuses people"s attention on Internal Processes rather than results
- there is not enough focus on what the customer actually wants.
2. TQM focuses on minimum standards – products are being made with no defects, but they also have no "Wow" factor. I.e. Fords look like Nissans, Look like Toyotas etc.
3. TQM develops its own cumbersome bureaucracy – A Quality department that grows and grows in size producing paperwork that chokes the business.
4. TQM delegates Quality to Quality Czars and experts rather than to real people – responsibility is taken from those who should have it, i.e. everyone, quality can"t be delegated.
5. TQM does not demand radical organisational reform – to often this is an excuse
downsizing rather than freeing up people from fire fighting to becoming experts and acting across boundaries.
6. TQM does not demand changes in management compensation – payment of bonuses depending on short-term profit is still the main bonus measure (80% of organisations).
7. TQM does not demand entirely new relationship with outside partners – sole supplier status is often misused to hold that supplier to ransom, rather than using support, trust and caring about the well being of your partners to improve the whole supply chain.
8. TQM appeals to faddism, egotism and quick fixism – TQM is often sold as a quick fix. Many managers are not capable of staying the course in this never-ending process; many lose the plot and become obsessed with the Baldrige Award.
9. TQM drains entrepreneurship and innovation from corporate culture - Companies need to be more chaotic to make the big breakthroughs and this does not fit with "Do-it-right-first-time". People will accept the imperfect if there are other compensations. Ferrari makes impractical cars that leak oil and breakdown a lot but they sell.
10. TQM has no place for love – TQM is clinical, analytically detached, sterile and mechanical. There is no emotion or soul. "You have no right to manage unless you talk passionately about what you are doing. "Debbie Coleman Apple.
11. TQM is sold and implemented as a formula to solve all your problems – TQM should be kept in perspective, it is tqm not TQM! It won"t, and can"t, solve every problem
Recommendation"s
Agrotran should adopt TQM as part of their business strategy. They should be clear on why they want to do this – long-term profitability, increase market share etc., and tailor their approach.
There are a number of tasks Agrotran should under take in this process:
1. Establish a TQM team to oversee the projects and training. This should be made up of the senior management, it is important that management understand and is committed to TQM. It should include someone from Nat-truk who has experience in this area, and Tom Smith as the most vocal critic to act as "devils advocate" and to win his commitment back which seems to have taken a knock.
2. Establish the reasons for change and communicate this to all involved
3. Create a Vision statement that encapsulates what the company is trying to achieve and how it intends to achieve it. In all the different activities this will provide everyone with a common focus
4. Establish the standard they intend to supply with reference to customer requirements the capabilities of the company and its suppliers.
5. Carry out a health check to establish their current position, what areas are in most need of improvement, what situations are constant problems, e.g. The communication problems over process etc.
6. Set up a system that will collect data and establish the costs of failure and the reasons behind this.
7. It would probably be worthwhile reviewing their Quality System (ISO9000) as this seems to be Nat-Truk"s imposed on Agrotran. This should be mainly under the control of Agrotran as it will be based on their knowledge of how Agrotran works best and their knowledge of their current customers requirements, Nat-truk would have more input, but not take over, when it comes to their areas of expertise.
8. Use the previous step to draw a quality strategy, to include; Goals, required systems and tools, behaviour changes to create a suitable culture in the company, resources required. Create a timetable and priorities for the definable projects. Some projects should be aimed to be completed soon, so that changes can be seen.
9. Establish the requirement and time table for training and education
10. The senior management should also keep themselves up to date with the current developments, debates and criticisms of TQM. After all TQM does practice what preaches "continuous improvement" and this can help the company in their own continuous improvement.
References
Crosby PB. (1979) Quality is free, The art of making quality certain McGraw-Hill
Dale, BG. (1999) Managing Quality – Third Edition Blackwell Business
Feigenbaum AV. (1991) Total Quality Control, Third Edition Revised, 40th Anniversary Edition McGraw-Hill
Gordon, J. (1994) An Interview with Joseph M Juran. (advocate of total quality management) Training, May 1994 v31 n5 p35
Grint, K. (1997) TQM, BPR, BSCs and TLAs: managerial waves or drownings? (total quality management; business process reengineering; just in time; balanced score cards; three-letter acronyms) Managerial Decision, Sept-Oct 1997 v35 n9-10 p731
Grossman, SR. (1994) Why TQM doesn"t work…and what you can do about it. (Total Quality Management) Industry Week, Jan 3, v243 n1 p57
Harari, O. (1992,1997) Ten reasons TQM doesn"t work (reprint, best of the cutting edge) V86 Management Review, 01-01-1997
Harari, O. (1993), The eleventh reason why TQM doesn"t work. (Total Quality Management) Management Review, May 1993 v82 n5 p31
Hiam, A. (1994) Does Quality Work? A Review of Relevant Studies The Conference Board. New York
The Institute of Management, Total Quality: Mapping a TQM Strategy, Checklist 029, Institute of Management
The Institute of Management, Preparing for ISO9000, Checklist 004, Institute of Management
Juran, JM. & Gryna, FM. (1988) Juran"s Quality Control Handbook 4th Edition
Kaye, M & Anderson, R. (1999) Continuous improvement: the ten essential criteria International Journal of Quality & Reliability Management, v16 n5 p485
Bibliography
Beckford, J. (1998) Quality – A critical introduction Routledge, London & New York
Beecroft, GD. (1999) The role of quality in strategic management Management Decision, v37 i6
BSI (1990) BSI Handbook 22 – Quality assurance British Standards Institute
Conti, T. (1999) Vision 2000: positioning the new ISO 9000 standards with respect to total quality management models. Total Quality Management, July 1999
Easton, GS. & Jarrell, SL. (1998). The effects of total quality management on corporate performance: an empirical investigation. The Journal of Business, April 1998 v71 n2 p253
Fülsher, J. & Powell, SG (1999) Anatomy of a process mapping workshop The Journal of Business, v5 n3 p208
Harrington, JH. (19990 Performance improvement: a total poor-quality cost system The TQM Magazine v11 n4 p221
Heaphy, MS. & Gruska, GF. (1995) The Malcolm Baldrige National Quality Award – A Yardstick for Quality Growth Addison-Wesley Publishing Company
Holland, R. (1997) TQM & STW Combine as the twin thieves of individualism Richmond Times-Despatch Wed July 9 1997
Kanji, GK. (1998) Total quality management – models Total Quality Management, Oct 1998 v9 i7 p633
Küger, V. (1999) Towards a European definition of TQM – a historical review The TQM Magazine v11 n4 p257
Laszlo, GP. (1999). Implementing a quality management program – three Cs of success: commitment, culture, cost The TQM Magazine v11 n4 p231
Lee, TY. Leung, HKN. & Chan KCC. (1999). Improving quality management on the basis of ISO 9000 The TQM Magazine v11 i2
McAbe, D. & Wilkison, A. (1998). The rise and the fall of TQM: the vision, meaning and operation of change. (total quality management) Industrial Relations Journal, March 1998 v29 n1 p18
McAdam, R & O"Neill, E. (1999) Taking a critical perspective to the European Business Excellence Model using a balanced scorecard approach: a case study in the service sector Managing Service Quality v9 n3 p191
McCormack. SP. Lewis, KJ. Mink, O. & Batten, JD. (1992) TQM: getting it right the first time Training & Development June 1992 v46 n6 p43
McFall, M. (1987) Expert systems – Computer-aided quality assurance Quality Sept 1987
Malone, MS. (1997) A way too short history of fads. (business and management fads) Forbes, April 7 1997 v159 n7 p71
Management Scotland (1999), Quality Scotland"s Vision Issue 14 September/October 1999, The Institute of Management
Marsh, J. (1996) The Quality Toolkit – A practical resource for making TQM happen
Marsh, J. (1995) A proliferation of Quality Initiatives Total Quality Partnerships http//www.tqp.com
Masson, R. (1999) Quality in Scotland The TQM Magazine V11 I1
Mohanty, RP. (1998) Understanding the integrated linkage: Quality and productivity Total Quality Management, Dec 1998 v9 i8 p753
Romano, C. (1994) Report card on TQM Management Review Jan 1994 V83 n1 p22
Seddon, J. (1989) A passion for quality Total Quality Management, May 1989
Taylor, L. (1993) Quality Street (Total Quality Management) New Statesman & Society, Oct 22, v6 n275 p25
Wilkes, N. & Dale, BG. (1998) Attitudes to self-assessment and quality awards: A study in small and medium-sized companies Total Quality Management Dec 1998, V9 i8 p731
Wilkinson, A & Willmott, H. (1996) Quality management, problems and pitfall: a critical perspective International Jounal of Quality and Reliability Management Feb 1996 v13 n2 p55
Xie, M. & Goh, TN. (1999) Statistical techniques for quality The TQM Magazine v11 i4
Other sample model essays:
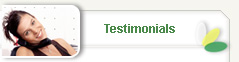

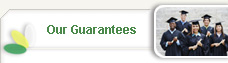

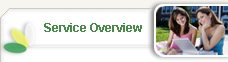

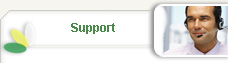

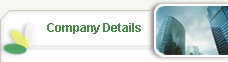
